Plastic and tyre are used in thousands of different ways. In fact, it won’t be wrong to say that it is difficult to imagine modern society without various plastic and tyre products. Plastic and tyre are cheap and highly durable. However, one of the biggest disadvantages of this durability is that it degrades very slowly with. Natural processes take thousands of years to degrade the plastic. The small pyrolysis plant is an effective way to deal with this problem.
It is estimated that over 1 billion tons of plastic and tyre waste has been discarded since the 1950s and that waste is expected to persist for hundreds or even thousands of years. This plastic waste has filled landfills and is also the cause of land pollution and water pollution as various chemicals in the plastic products leech in to the ground water and pollute the groundwater. So finding a solution to recycle waste plastic becomes important.
Over the years, researchers have been trying to find a way to get rid of this huge amount of plastic waste in the right manner. One of the most effective and profitable ways of converting plastic waste into useful products is Beston pyrolysis technology. Pyrolysis technology may be defined as chemical decomposition of organic substances at high temperature and pressure. Anhydrous pyrolysis is a highly effective way of producing liquid fuel similar to diesel from waste plastic. Beston Company is a available source to get different pyrolysis reactor types.
Use Waste Pyrolysis Plant to Tyre and Plastic in A High Efficiency
Waste plastic is heated at a temperature of 400 to 450 degrees in the absence of oxygen in the waste tyre and plastic pyrolysis plant. The process of pyrolysis results in breakdown of longer chain molecules in to short chain molecules. The process is similar to the natural process through which carbon is converted into oil by nature though this process takes millions of years. In the case of pyrolysis process, this process is carried out under intense heat in a closed system and the longer chain polymer molecules break down into shorter chain polymers under intense heat and pressure.
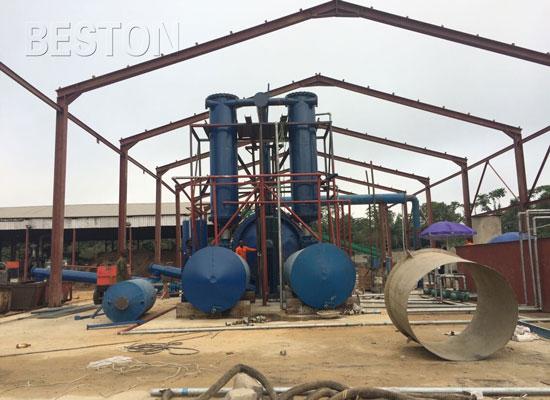
There are a number of manufacturers supplying a wide variety of plants with capacity ranging from three tons per day to 48 tons per day. Some of the manufacturers also supply plants with much higher processing capacity. Most of these plants are highly efficient and are capable of converting more than 95% of waste plastic into useful products.
In the pyrolysis process, around 45 to 50% of the raw material is converted into fuel oil. This fuel oil can be used in various industrial processes. It can be converted into diesel or used as heating oil or as a fuel directly. Another product of the pyrolysis process is carbon black. The carbon black generated through this process is much cheaper as compared to the carbon black generated from petroleum. Around 30% of the raw material is converted into carbon black in this process.